What is the Eden Project
The facts:
The world’s largest man-made complex of greenhouses in Cornwall, United Kingdom.
Total surface | 39.540 m2 |
Total steel weight | 700 tons |
Total length off all beams | 36000 m |
Steel weight per surface | less than 24 kg/m2 |
Biggest hexagon area | 80 m2 at a span of 11 m |
Biggest dome diameter (dome B) | 125 m |
Column free area | 15590 m2 WTB and 6540 m2 for HTB |
Official website: www.edenproject.com
You can read on or jump to a series of videos at the end of the page, explaining what the Eden Biodome is.
The following is a transcription of a PDF entitled “The structural making of the Eden Domes” by KLAUS KNEBEL, JAIME SANCHEZ-ALVAREZ, STEFAN ZIMMERMANN, MERO GmbH & Co. KG, D-97084 Würzburg, Germany
INTRODUCTION
In the spring of 2001, on the south-western tip of England in Cornwall, the Eden Project was opened to the public. This project is, along with the dome and the ferries wheel in London, one of the largest British millennium projects. In an outdoor area of 15 ha, and in two giant greenhouses, the modern Garden of Eden presents different climate zones of the world with their typical vegetation. The steel structure of the two huge domes was developed from the MERO space frame system: pipes are bolted together by means of nodes. Due to very low tolerances and quick assembly, economical structures can be realised even for complex geometrical configurations. Very light and transparent, but also durable air filled foil cushions were chosen for the cladding system. A cushion system of this size had never been built before. The 125 million Euro project is a great success. Since the official opening in March 2001, thousands of visitors take pleasure in the gardens every day. The Garden of Eden has been called the eighth wonder of the world by the British press.
DESCRIPTION OF THE COMPLEX
The complex consists of several parts (Fig. 1 and Fig. 2). Beside the outside area there are 4 main buildings. The entrance is located at the top of the clay pit. Here, several souvenir shops, restaurants and exhibitions are located. This building was completed and opened to the public about one year before the opening of the rest of the complex. About half a million people visited the Eden construction side during May 2000 and the official opening in spring of 2001 and watch as the complex grew. The main building complex consists of three parts. The biggest part is the Humid Tropic Biomes (HTB). Here plants from the subtopic part of the world like West Africa, Malaysia or Oceanic are shown. The HTBiomes are comprised of 4 domes (ABCD) and the dome B is the biggest one of all. The diameter is almost 125 m and the free height inside is close to 55 m so that even big jungle trees have enough room to grow up. Since these plants need the most sunlight to grow, the location of these domes were located by the architects so that they catch the most sun power.
The other four Domes (EFGH) form the Warm Temperature Biome (WTB) with an internal length of about 150 m, width 56 m and a height up to 35 m. Here the typical plants of the dry and warm areas like south Africa, California or the Mediterranean area are located. The humidity and temperature is not as high as in the HTBiomes. These two domes are connected by the Link building which is covered by a grass roof and is therefore almost invisible from the surface. The link building is the entrance to the Biomes. Beside sanitary facilities the visitor can have a rest in restaurants. The central outside area is about 15 ha big. Outside many other plants from different areas of the world can grow due to the mild clime of Cornwall without shelter. Many other varying attractions and exhibitions make the Eden Project an attractive park for the visitors.
STRUCTURAL CONCEPT
The first layout made by the architects of Nicholas Grimshaw and Partners (NGP) together with the engineers of Anthony Hunt associates (AHA) [1] was similar to the London Waterloo train station (Fig. 3A). Arches and purlins are the basic steel structure for the glazing elements. The disadvantage of this layout was the high steel weight and the small glass elements which blocked too much sun light. Although this concept was difficult to fit to the varying natural surface of the clay pit. After McAlpine was chosen as general contractor, it was also clear that this steel structure was too expensive to realise. Another concept had to be found. The architects and engineers of NGP and AHA then developed a single layered domes structure based on a hexagonal geometry (Fig. 3B). This layout had several benefits. It is easier to fit the structure to the ground surface and the size of the hexagon elements allows more sun light to enter.
The visual appearance a hexagonal geometry is also close to many object found in nature. The next question was how to realise this structure on an economical basis. In 1997 MERO joined the Eden Project. MERO has realised many complex structure in the past decades all over the world. After some preliminary studies it was found, that the single layered structure in this large dimensions could not be build economically and that the deformation were too large. Working closely with NGP and AHA, the geometry and structure was modified by MERO. The result of this optimisation was a double layered structure with the characteristic hexagonal top chord geometry (Fig. 4). As a cladding system of air filled EFTE foil cushions was chosen. The very low weight of this material in contrast to glass allowed a further reduction of the necessary steel weight. This foil material allows much more UV light to pass into the Domes and also provides good heat insulation. This structural concept fulfilled all the required points. The weight and amount of the steel was minimised, the surface cladding was transparent for the sunlight, the entire interior area is free of columns, the optical appearance is attractive and the structure is economical and fast to be build. In the spring of 1999 MERO began with the final technical design for this unique project.
GEOMETRY
The Eden domes are geodesic spherical networks. They are “spherical” because the elements of a network, normally the nodal points, lie on the surface of a sphere. These grids are called “geodesic” because they have the form, structure and the symmetry properties of the geodesic domes known through Buckminster Fuller, where not all the members follow true geodesic lines. Strictly speaking, geodesic lines are curves on any kind of surface and, from the innumerable lines that can connect two points on the surface, they represent the shortest distance between the two points. In the common geodesic domes, however, structural members are normally made straight, not curved, and only their end points, usually the centres of physical connectors, lie on the surface of a theoretical sphere.
Some other ways to project or map networks on spherical surfaces have been developed by Emde [2] in Germany, Fuller [3] in America and Pavlov [4] in Russia. The majority of spherical geodesic networks in building practice are derived from the platonic solids icosahedron and dodecahedron. An icosahedron is a regular polyhedron with twenty identical faces, which are regular triangles. A dodecahedron is a regular polyhedron with twelve identical faces, which are regular pentagons. Dodecahedron and icosahedron are duals from each other. If the midpoints of adjacent faces of a polyhedron are connected with lines, the resulting body is the dual of the first one and vice versa. It should be noted that the two polyhedrons placed as duals have a common centre and they can also be positioned concentrically within a circumscribing sphere. Thus, a geodesic network can be obtained by projecting or mapping in a prescribed way the tessellated faces of the polyhedron onto the surface of the sphere.
GENERATION OF THE GEOMETRIC MODEL
The structural network of a dome in the Eden Project consist of two concentric spherical networks with a prescribed radius difference or structural depth between them. Here, external and internal networks are interconnected with a set of lines called diagonals, thus giving rise to a double-layered spherical network with a three-dimensional carrying behaviour. The external grid is a hexagonal network, here referred to as “Hex-Net”, whereas the internal grid consists of triangles and hexagons and is consequently called “Tri-Hex-Net”.
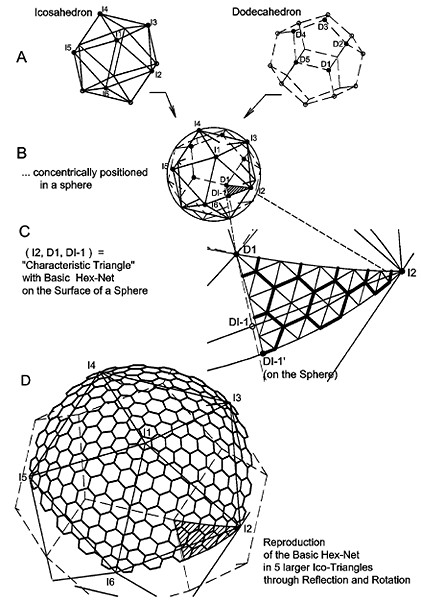
Figure 5
The key steps to generate the Eden-geometry, which are dodeca-ico networks, are shown in Fig. 5 and reference [3]. In order to generate a dodeca-ico (DI-) network, the two polyhedrons have to be placed as “duals” with respect to the centre of a sphere. The corners or vertices of the icosahedron in the resulting network can be recognised by their pentagonal symmetry and they correspond with the midpoints of the dodecahedron’s faces.
In Fig. 5 a so called “characteristic” triangle (after Emde, [2]) is defined by the icosahedron point I2, the dodecahedron point D1 and the icosahedron’s edge midpoint DI-1’ projected on the surface of the sphere. This triangular surface region is the smallest symmetry part of the whole spherical network. In English speaking countries, this triangle is often known, after Fuller, as the “lowestcommon-denominator-” or LCD-triangle. Through this approach, it is possible to subdivide the spherical surface in 120 minimal symmetry parts. The actual specifications of geometric and connectivity properties of the whole network can thus be reduced to this minimal triangle.
In the Eden domes, the hexagons were obtained by omitting the appropriate elements of the minimal triangular net. The complete hexagonal network was subsequently generated by reflections and rotations on the surface of the sphere of the minimal network within the characteristic triangle.
The internal tri-hex net is obtained from the corresponding elements in the characteristic triangle. Here, the nodal points of the internal grid are derived from the external line midpoints which have been projected concentrically onto the theoretical sphere carrying the internal grid. The tri-hex net is then generated by connecting the points corresponding to adjacent lines of the hexagonal grid. The inter-layer diagonals are obtained, in turn, by connecting every internal point with the corresponding endpoints of its external source line.
The resulting spatial network strongly resembles the molecular organisation of certain minerals, like the silicates (SiO4) as seen in Fig. 6. Among other properties, these natural crystalline formations present minimal energy paths with minimal material consumption. Similarly, the three-dimensional geometric arrangement of the Eden domes makes possible an economic structure with a visually attractive appearance.
PLANARITY OF THE HEXAGONS
The hexagons of geodesic domes, unless special measures are taken, are not normally plane. The selected cladding of foil pillows required the hexagons to be as planar as possible in order to facilitate the construction and assembly of the supporting edge frame and to prevent unplanned folding and wrinkles on the pillows. Based on the works of Emde [2], Fuller [3] and Pavlov [4], a special algorithm was developed to obtain hexagons as plane as possible within tolerable fabrication and installation deviations. “Tolerable” means for the Eden domes that a point can be 60 mm out of the average plane of the largest hexagon, which has edge lengths of up to 5.20 m.
A further “flattening” of the hexagons would mean losses in the uniformity of the networks, which is measured as the ratio between the maximal and the minimal length of a grid. As an orientation, very homogeneous DI-geodesic networks have uniformity quotients of about 1.2, while the Eden networks vary around 1.26. Furthermore, alternative networks for the Eden domes with perfectly plane hexagons yield uniformity quotients of up to 2. In these extreme cases, that correspond to the finer subdivided networks, hexagons along the edges of the basis icosahedron tend to present larger distortions with the corresponding disadvantages for the structural system and a disturbing visual effect.
STATICAL CALCULATION
After the final design of the geometry, the calculation of the steel structure was done. The geometry was transferred into a statical 3D computer model (Fig. 7). The calculation was carried out using the 3D analysis program RSTAB [5] based on second order theory. The top cord elements and the arches are beam elements, the bottom cord and diagonals are modelled using truss elements. The basic load cases and load combination are according to BS 5950. Due to the mild climate in Cornwall the basic snow load is only 0.3 kPa. The results of the wind tunnel test performed at BMF Fluid Mechanics LTD. in London showed, that due to the form of the clay pit, the wind is acting mostly as suction onto the Biome structure.
In addition to the ordinary loads cases, some extraordinary load patterns had to be regarded. In the valleys of the cushions and especially in the valleys of the arches, drifting and sliding show can occur. Local snow loads up to 1.2 kPa were considered which resulted in some extra cables supporting the cushions in the area of the arches.
A cushion that loses it’s air pressure could result in a water filled area in the case of rain. Local load up to 250 kN per hexagon were considered for this case. The performed analysis proved the stability of the structure even when some members failed. The governing load case for the design was mostly the snow and snow drift load case. Changes in temperature are usually not critical for the stress design of dome structures since they can expand freely in radial direction. Also, support movements are causing no major forces. Therefore, the domes of Eden are build without any expansion joints.
THE BOWL NODE
The main design parameters for the connection in the top chord were :
• Rigid Connection for the three tubes with d=193 mm • Hinged connection for the three diagonal members • Fast and easy erection
• Minimum tolerances
• No side welding
• Possibility to fasten a rope for mounting the domes on the outside
• Architecturally pleasant
As a result of these requirements, a so called bowl node was chosen (Fig. 8). This type of node is an enhancement of the node type used by MERO when circular or rectangular hollow tubes are joined together by bolts. The top of this connection is even with the pipes, so that the cladding can be put right on top of it. The bowl node is made out of cast iron (GGG40) and the weight is about 80 kg. The diameter of the 1100 nodes is about 400 mm and the wall thickness is 40 mm. Each node was cut and drilled by a computer aided machine which limited the tolerance to a minimum.
TOP CHORD BEAMS
The stress design of the top chord resulted in a tube diameter of 193.7 mm. In order to use the same connection to the node, all top chord pipes are the same diameter, but with different wall thickness according to forces and buckling length. Since all the necessary geometrical angles to form a dome are put in the node, the ends of the top chord beams are cut rectangular which allow fast and efficient manufacturing.
At each end, an end-plate is welded and at the top of the beam a erection hole cut (Fig. 9). High strength pre-stressed bolts (M27 and M36) were used for the connections of the beams to the bowl node. An additional bold M16 was used to fix the beam in it’s right position and to transfer torsional moments. On top of the beams short brackets were welded which support the aluminum framing for the cushions.
BOTTOM CHORD AND DIAGONALS
The bottom chord tubes and diagonals are made of the classical and well known MERO space frame system. The performed stress and stability design lead to diameters between 76.1 and 168.3 mm. According to the BS Standard the buckling length was limited to 180. They are designed and manufactured according to the MERO technical approval [6]. The connections in the bottom layer are also classical MERO space frame nodes (Fig. 10) which allow a fast and easy erection of the structure.
THE ARCHES
Along the intersection of the domes a triangular truss girder is applied. The span is up to 100 m for the biggest one. The sections of the arches measure 219.1 mm for the top beam, 159 mm for the two bottom beams and 101.6 mm for the diagonals. The top and bottom chord beams are bent. For manufacturing, the girders were welded in three pieces and after setting up the rest were welded on site. The arches rest hinged supported on heavy foundation concrete blocks. On top of the 219 mm tube a 10 mm steel plate was attached to form and fix the gutter. The connecting arches are flush with the dome top and bottom surface, and therefore, do not interrupt the flow of the design
SUPPORTS
A challenging point was the design of the support system. Because the 800 m long foundation varies, each of the 187 support points is geometrically different. The supporting construction also consists of tubes with diameters of 193 mm which are welded together . The connecting top chord beams and diagonals are bolted together. The base plates are fixed to the foundation by anchor bolts M27 and M36 and the horizontal forces are transferred by shear blocks.
DOORS AND VENTS
To achieve the tropical climate inside the domes, a special ventilation system had to be used. The required openings were determined by Ove Arup & partners , London. On top of each of the 8 domes are vent openings. The 5 hexagons surrounding the top pentagon were divided into 3 triangles so that each dome has 30 openings operated by remote control. These windows are also covered by triangular air cushions.
The substructure consists of rectangular hollow sections 140 x 70 mm. For the air inlet glass lamella windows are arranged around the edge of the domes (Fig. 13). Warm air can be blown inside the domes using heaters. Each dome also has some doors for maintenance and emergency exits only. The access for visitors is through the link building only. For maintenance the vents on top of each dome has a cat walk.
MANUFACTURING
Most of the steel structure was manufactured in the MERO workshop close to Wuerzburg in Germany. Only the arches and support point were fabricated elsewhere. The manufacturing of the MERO beams and nodes was done using a computer aided machine. The end plate and support brackets of the top chord beams were welded by hand. Each element and node has it’s unique number which remained the same during the design, manufacturing and erection phase.
For corrosion protection all steel elements are hot dipped galvanized. Due to their sizes the segments of the arches were galvanized by a company in France, which has one of the biggest galvanizing tubs in Europe. The bowl nodes made out of cast iron GGG40, were also galvanized. With a general inspection every two years, the steel structure is designed to be maintenance free for 30 years.
CLADDING
The more than 800 hexagon elements are covered by air filled cushions. These cushions are made of transparent EFTE (Ethyltetrafluorethylene) foil. The basic material is between 50 µm and 200 µm thick with a width of 1.5 m. The foil material was cut and welded. The normal cushions are made up of three layers. The top and bottom layer form the cushion and carry the loads. An additional layer between them has the function of enhancing the temperature insulation and also dividing up the airspace in case of leakage. In areas of high local wind suction the outer surface of the cushions was strengthened by using two layers of foil.
The cushions are attached on an aluminium frame to the top chord beams. Each cushion is also attached to an air supply system (Fig. 15). The pressure inside the cushion is about 300 Pa. The maximum height of the inflated cushion is about 10 to 15 % of the maximum span (Fig. 16)
Material EFTE has been used for more than 20 years. It is extremely light and transparent. The surface is also quite smooth so that the dirt on the outside is washed down by the rain. Cushions in this project size had never been built. During the design stage, extensive studies and tests were performed by MERO, the consultant Ove Arup (London) and the foil subcontractor Foiltec in Bremen (Germany). Some of the tests were performed on a real 1 to 1 scaled model. The results of this studies lead to the important parameters for the design of the cushions with spans up to 11 m. In areas of high show load, like the arches, some additional cables were needed to support the cushions. After the design phase, the size of each of the 800 elements was calculated, cut, an manufactured. The gutter construction between the single domes is made out of insulated aluminium parts and is covered on the outside by foil. The rain water is saved and used for the plants inside the Biomes. The entire roof surface can be maintained by abseilers using ropes attached to steel pins which are attached to each bowl node of the structure (Fig. 8).
ERECTION
The erection of the steel structure began in November 1999. Extensive ground movement and the building of the 858 m long concrete foundation was done by the general contractor. The foundation is 2 m wide and 1.5 m high. It rests on up to 12 m long concrete piles which were drilled into the ground. For the erection of the structure, a scaffolding was set up. This scaffolding has it’s place in the Guinness book of records as the biggest and tallest free standing scaffolding of the world. Most of the hexagons are put together on the ground and then lifted into place by tower cranes and then bolted together (Fig. 17). The prefabricated pieces for the arches were about 13 m long. They where also set up on the scaffolding and then welded together. After the erection of the steel structure was done, the scaffolding was removed. The installation of the foil cushions was done by abseilers (Fig. 14). The ground work inside the Biomes could be done parallel to the cladding work. The cladding was finished on time in September 2000 so that the Biomes could be heated and the planting could commerce during the winter. The Eden project opened the doors for public in time in March 2001. For further information see www.edenproject.com and www.eden-project.co.uk
THE MAIN STRUCTURAL DATA
Total surface 39.540 m2
Total steel weight 700 tons
Total length off all beams 36000 m
Steel weight per surface less than 24 kg/m2
Biggest hexagon area 80 m2 at a span of 11 m
Biggest dome diameter (dome B) 125 m
Column free area 15590 m2 WTB and 6540 m2 for HTB
PARTICIPANTS
Client: The Eden Project (www.edenproject.com)
Architect Nicholas Grimshaw & Partners Ltd, London (www.ngrimshaw.co.uk)
General Engineer Anthony Hunt Associates, Cirencester (www.anthonyhuntassociates.co.uk)
Bauphysik Ove Arup & Partners, London (www.arup.com)
Wind channel test BMT Fluid Mechanics Limited London (www.bmtfm.com)
General Contractor McAlpine JV (www.sir-robert-mcalpine.com)
Steel & Cladding MERO GmbH & Co.KG, Würzburg (www.mero.de)
subcontractor : Foiltec GmbH, Bremen (www.foiltec.de)
REFERENCES
[1] ALAN C. JONES : Civil and Structure Design of the Eden Project,
International Symposium on Widespan Enclosures at the University of Bath,
26-28 April 2000.
[2] EMDE H.: Geometrie der Knoten-Stab-Tragwerke :
Veröffentlichung des Strukturforschungszentrums Würzburg 1978
[3] FULLER R.B. : In : The Dome Builder’s Handbook :
Edited by John Prenis; Running Press Philadelphia Pennsylvania ; 1973
[4] PAVLOV G.N.: Determination of Parameters of Crystal Latticed Surfaces Composed
of Hexagonal Plane Facets ; Int. Journal of Space Structures ;
Vol.5 Nos. 3 & 4 1990 Multi-Science Publishing
[5] RSTAB 5 : Ingenieursoftware Dlubal GmbH http://www.rstab.de
[6] MERO technical Approval ; Z-14.4-10 erteilt vom DIBT Berlin
[7] KLIMKE H., How Space Frames Are Connected, IASS Madrid 1999, pp B4.13 – B4.19
[8] KLIMKE H.: Entwurfsoptimierung räumlicher Stabstukturen durch CAD-Einsatz,
Bauingenieur 61 (1986) Seite 481 bis 489
[9] LEHNERT S.: Das Eden Projekt ; Intelligente Architektur; Ausgabe Nov/Dez 2000
The Eden Project
|
The Eden Project
|
Millennium Now – Eden Project, Cornwall
|
Bristol – The Eden Project.mov
|
EGS Energy Geothermal Plant – The Eden Project
|
Eden Project Biomes, St Austell, Cornwall
|
Rainforest Biome, Eden Project
|
Live footage of Eden Project flooding
|
Project Eden: A Documentary
|
Eden Project co-founder Tim Smit's business advice
|
Eden Project: 'More than just architecture, it's about relationships'
|
Eden Project: Green Build Cornwall, April 2011
|